My D.Sc. research very briefly
Hi all! In a few weeks, I’m presenting my doctoral research in a small seminar. For that, I had to squeeze for years of work into one A4. Which is completely doable – everyone should be able to communicate their core points without wasting an hour of everyone’s time. Anyways, I though I’d share it here. So, enjoy the basics on eddy and circulating currents, and why they matter:
Background and Motivation
The requirements placed on electric motors and generators have grown dramatically in the last decade. Partly, this is due to the increasing interest in energy efficiency. Indeed, almost all electrical energy is produced by generators, and roughly 40 \% of it is then spent in electric motors. Thus, even a modest improvement in efficiency will have a significant impact on the global scale. Correspondingly, stricter and stricter efficiency standards are being placed on new machines.
On the other hand, novel operating environments such as electric vehicles demand high performance from the machines. Indeed, electric vehicle motors typically have power-to-weight ratios an order magnitude higher than usually seen in the more industrial applications, or gasoline engines for that matter.
High efficiency and performance are both closely tied to the losses of the machine. Reducing the amount of energy wasted obviously improves the efficiency, but it also allows the size of the machine to be reduced. Thus, understanding and modelling the losses is crucial for meeting these dual goals.
Losses in Electrical Machines
Typically, even more than 60 of the total losses occur in the current-carrying conductors in the machine, i.e. windings. A part of these resistive losses can be explained by the well-known equation. However, the presence of time-varying flux density
complicates the matter.
Indeed, the current density is typically unevenly distributed over the cross-section of any winding conductor. This eddy-current phenomenon increases the resistive losses, proportionally to the height of the conductor. Thus, several parallel-connected smaller conductors are typically employed, called strands.
However, in this case the total current is often unevenly distributed between the strands. The term circulating currents refers to this phenomenon. Again, the losses are increased, even if the current density inside any particular strand were close to uniform.
High-Performing Finite Element Analysis
Due to the complex nature of the circulating and eddy currents, numerical finite element analysis (FEA) is typically used to model them. The geometry of the problem domain is divided into small elements (typically triangles). An approximating function space is then constructed based on the elements.
However, the complicated geometry of a typical winding results in a very high number of elements, as illustrated in Fig. 1. This leads to long computation times, usually in the range of hours or even days.

Several high-performing numerical algorithms were proposed in the doctoral thesis to solve this problem. Significant speed-ups were obtained, e.g. reducing a time-stepping analysis time from 10 hours to 7 minutes. Nevertheless, a very good precision was maintained, with error norms in the order of .
Stochastic Modelling
Another complication is related to the manufacture of the windings. Especially when round wires are used, their positions vary greatly between different machines, in a stochastic fashion. Correspondingly, such a winding is called random-wound.
Based on a large set of measurement data, a sampling algorithm was developed to model this random process. Some results are illustrated in Fig. 2. The thick curve shows the measured loss distribution, while the thin line illustrates the simulated results. As can be seen, a very good agreement has been obtained, considering the complexity of the underlying phenomenon.
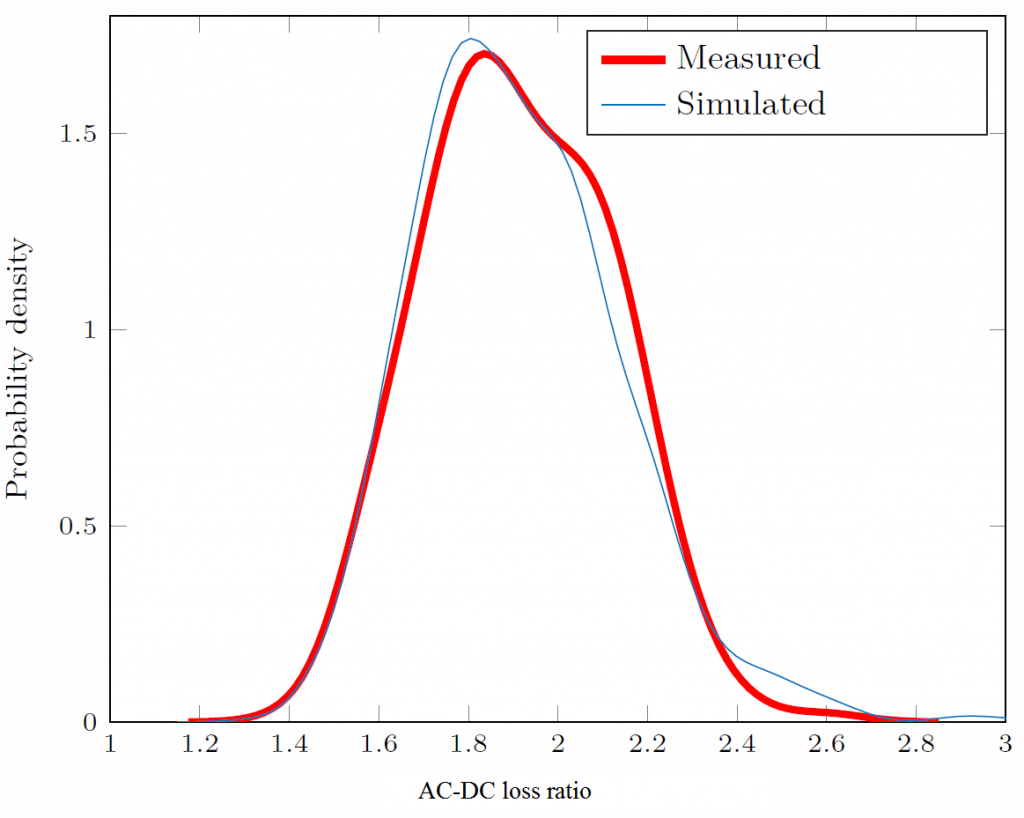
-Antti
Check out EMDtool - Electric Motor Design toolbox for Matlab.
Need help with electric motor design or design software? Let's get in touch - satisfaction guaranteed!
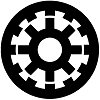