Developing high-performance electric motors for aircraft
Saw my earlier post about electric aviation? Today, we’re continuing on the same topic, by means of an interview.
Nicola Chiodetto was once my student for a while, making his Master’s thesis about circulating currents. Today, he’s a PhD student in Newcastle, developing superpowered electric motors for aircraft. Tomorrow, he’ll probably be the boss of you and me both.
At more than 3000 words, this is the longest post on this site so far. But, I really recommend you act like an actual responsible adult, and take the 10 minutes or so to read. It’ll be well worth it, I promise.
So let’s begin.
Basics
Q: Hi Nicola! I obviously know you, but most people reading this won’t. So for their benefit, can you tell us a little something about yourself first. What are you doing right now?
A: Hi there! My name is Nicola Chiodetto. Proudly belonging to the Italian folk that inhabits the homonym peninsula in the center of the Mediterranean sea. I hold a Bachelor in Energy Engineering and a Master in Electrical Engineering. I pursued them both from the University of Padova. It is a very small, but beautiful, town in the North East of Italy. If you are familiar with Venice, Padova is just 50 km inland straight to the west.
However, I completed my studies in Boston University, USA and Aalto University, Finland, thanks to two exchange periods as an international student. Helsinki, well, better say Espoo, was the place where I met Antti. At the time, we are talking about 2015, he was a second year PhD student, in charge of instructing a young Erasmus (EU funded Exchange program) student throughout his Master Thesis, aka me.
As for now, I live in the UK. Specifically, I have settled down in Newcastle upon Tyne, last considerably big English settlement before entering in Scottish lands. I am chasing a PhD degree in Electrical Engineering at Newcastle University. To be precise, I am about to start my second year right now. Nonetheless, I must point out that, before coming to England, I have attempted a PhD in Italy, again University of Padova, from October 2015 until July 2016.
Q: Newcastle’s quite a stretch away from the sunny Italy. How did you end up there? Or put the other way, why did you choose to leave Padova?
A: Why did I ended up here is related to many reasons. The main one is that, since 2014, I have been fascinated by the Electrical Machines world. It started with the Electrical Machine Design course I attended in Padova. It built up progressively during my thesis, thanks to the collaboration with the Electromechanics guys in Aalto. As mentioned, I then decided to embark in a PhD research experience in Italy. However, I soon realized I wanted to build and touch a real design with my hands, as an engineer. In my opinion, personal one, this was not possible in Padova. That is why I chose to come where I am now. Again, personal opinion, I am more convinced I can here build, and possibly test successfully, what I am investigating.
Work
Background
Q: Alright, what about your research then? Can you tell us something about that, or are you dealing with top-secret stuff only?
A: My research focus could be formally summarized as “Electrical Motor Design of Aerospace Propulsion”. Saying these fancy words is probably not really helpful, even if it gives an idea. So I will try to: 1) state what the Aerospace Industry wants nowadays, 2) explain what I actually do and treat in my research.
Q: Alright! Let’s begin with the industrial needs you mentioned.
A: The aerospace industry nowadays has set new targets in terms of CO2 emission limits, NOx emission cuts, and noise reduction for civil air transportation. Achieving the goals decided is not possible with the current only fuel-based (aka turbo engines) technology available. New solutions are required.
At the moment the mainstream seems to be a BLI hybrid solution. BLI stands for Boundary Layer Ingestion. These boundary layers are air streams along the airplane fuselage. At the moment they are just a source of extra drag, but if accelerated, possibly at the rear/tail of the airplane, they could increase the thrust capabilities. This would increase the overall aircraft efficiency, and decrease fuel consumption.
The solution investigated at the moment regards electric motors positioned at the tail of the plane, driving one or several propellers or fans. The motors are fed by electrical generators directly driven by the turbo engine shafts (technology already established in the more-electric aircraft (see for instance Boing 787). At the end of the day: the industry (Airbus/Boeing) wants the lightest and most efficient motor available (more weight –> more fuel –> higher consumption).
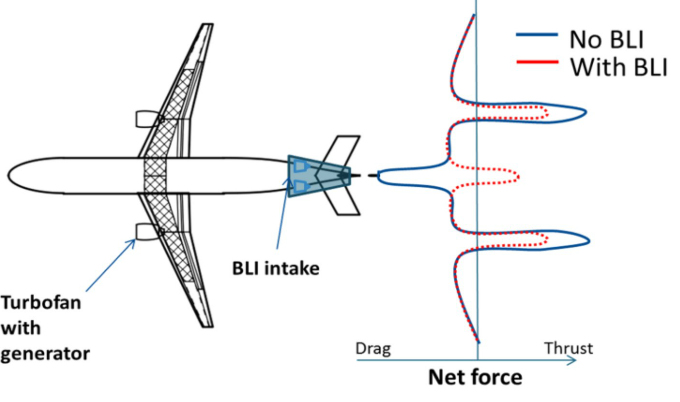
Meeting the demands
Q: I can really feel your point about the industry wanting to get everything at once. I mean, typically light weight and efficiency are somewhat contradictory goals. But moving on: what is it that you do, exactly?
A: What I do is related to the last aim addressed. Therefore, putting it easily: I need to find the best motor design which allows me a minimum weight with a very high efficiency. I am supposed to find this by analytical and software modelling, and experimentally. What I have done so far is creating a mechanical model for fast dimensional estimation of retaining components in the rotor of high speed electric motors. I have been doing this because high speed electrical machines are indispensable to reach good power densities (high power output for reduced weight). High speed is a broader term, that merits deeper and too long explanation, but for the moment I can tell you that “my” high speed is a design solution with around 250 m/s at the outer rotor radius.
Combined with a mechanically feasible rotor design I investigate the electrical machine losses in terms of torque capabilities and losses. I do this for different levels of current density imposed in the stator circuit.
Q: It’s good that you mention optimization, as I’m gradually shifting towards it as well. Anything you can tell me about it?
A: Honestly, the entire process is embedded in a structural optimization. In other words, I use an algorithm, derived from mathematical nonlinear programming theory, which “drives” my investigation towards good and feasible solution, in terms of efficiency and weight requirements. In other words, this automated process allows me to define the geometrical dimensions, which better fulfill the target.
Progress so far
Q: I took some courses on optimization during my Master’s. The main difficulty, I would say, is that many of the methods require the gradient of the objective function, something that is not readily available when numerical analysis is used. Partially for that reason, we often use some fancy genetic algorithm stuff here. But anyways, how would you describe your progress so far? I think I remember you saying that you almost gave up on permanent magnet motors and considered induction machines instead?
A: How is it going is a very tricky question. I am a perfectionist, so I would tend to say not very well, but that’s part of research first, and second for a design so challenging. Before mentioning the IM let’s see why I say this and what are the troubles.
Mechanical problems
Q: For the benefit of the audience, I can certainly attest Nicola’s perfectionist nature. So, when he’s saying things are “kinda okay”, I’ll be expecting some colossal breakthroughs withing the next few years, at least. But let’s move on to mechanics now.
A: By definition an electrical motor is an electromechanical device capable of converting electric energy into mechanical energy. Frequently electrical engineers forget that the main aim of this motor is to provide power at the shaft, to be able to spin something else! This is the scope! Said that.
Q: Quilty as charged…
A: In my case the mechanical design is an issue due to the very high stresses developed in the rotor components. I investigate Surface Mounted Permanent Magnet motors for the moment. They seem to give the highest torque/power density.
However, the magnets are just “dead” bodies, mechanically speaking, since they do not provide any retaining force, and they actually compromise the rotor integrity; although essential for the electromagnetic functioning. The design of a retaining bandage for preventing them from flying away is fundamental. However, a bigger, so stronger, sleeve “kills” the torque density of the machine.
So, a trade-off with the magnetic side has to be found. Also, is not sufficient to retain the PMs. It is essential to guarantee the torque transmission at all times: the PMs have to be touching the shaft, always. In case of attachment loss we have a lift off condition, which could cause eccentricity, rotor dynamics undesired resonances, and who knows what else….so again a compromise between lift off and “fly away”.
Q: It’s very nice that you brought up centrifugal stresses, as I’m doing a little magnetomechanical analysis nowadays, and they’re a big factor there too. But please continue. What are the sleeves made of, usually?
A: The best material in the market is carbon fiber. However, the UK company which usually winds up carbon fibers for rotors, is not able to provide me a pre-stressed bandage with my rotor dimensions. This is a huge issue at the moment for me. I need to find someone else capable to do so, before I start to build my machine.
Magnetic problems
Q: Aww that sucks. I mean, you’ve obviously made the necessary jump from pure theory to design, and you’re even taking into account the mechanical aspects which is something not all of us can say. And then your progress is sidelined by component procurement. Well, that’s life I guess. But enough about mechanics, let’s move on to electromagnetics. Any comments on that side?
A: Plenty. The frequency is a serious matter. Increasing frequency, (or rather, increasing the number of poles), reduces the core back thickness. For the same axial length of the machine the weight is reduced, too. Okay okay, it is not that simple, but the concept is broadly this.
That’s obviously good. However, the issues related to this solutions are multiple: the losses in the winding and also in the iron/core are almost in all the cases scaling up quadratically with the frequency. Considering that decreasing the weight means, almost always, decreasing the size/area of the machine, such a loss increase is not quite comfortable. On this point permit me to break a common stereotype: increasing speed does not automatically increase power density. At least not in term of rpm. The tangential speed in m/s is the one making the difference.
Q: Hmm I hadn’t thought it like that. But you must be right, power is (tangential) force times velocity, after all. But please continue.
A: Plus, as said, increasing the speed increases the losses quite considerably. So, usually a better cooling is needed, because the dissipation capabilities in terms of surfaces is sensibly reduced. Additional issues limits the frequency: the power electronics feeding the machine has limits for the switching frequency. Finally, the core back cannot be indefinitely thin, both in terms of physical manufacture and as stator core vibration modes (see again the mechanics comin’ back).
Thermal problems
Q: Which brings us nicely to the thermal problems. I have something of a love-hate relationship with them. On the other hand, pure heat flow is mathematically very simple, and easy to solve by numerical means. On the other hand, the variations are HUGE – nowhere else can you realistically expect to see a 10-fold difference in a (heat transfer coefficient). Plus of course the fluid flow stuff that goes hand-in-hand with thermal analysis is a nightmare. But please, carry on.
A: Thank you. From a very basic point of view the torque in the machine is proportional to the flux density (given in my case by the PM) and to the current density in the windings. Assuming the best PM available in terms of flux density we need the highest possible armature current to boost the torque. As it may be understood we have a limit because we don’t want to simply burn the machine. Or rewind it all over after every working cycle.
I can tell you that THIS IS THE LIMIT.
That is because a stronger material than the carbon fiber does not exist. A more energy dense magnet than NdFeB is not available. A higher frequency is not achievable from the switchers in Power Electronic converters. As a consequence, is easy to understand as the mechanical and electromagnetic limits are not really possible to overcome, unless new materials are “invented”/manufactured. BUT, thermally we can play, or at least try to play. Why so?
Q: …because you can at least increase the current density, if you cool stuff better?
A: Exactly. And furthermore, so far all the troubles described have not necessarily anything to do with aerospace: they could be just related to a super high power density machine for an “on the ground” application. I am saying that I can play more on the thermal side by using what the aerospace conditions are giving me. I mean, in high altitude we have:
- minus 50 degrees Celsius as standard air temperature
- super fast air stream (high velocities)
Said that, it would be already a great achievement realizing a design fully cooled with forced air, but with the same power densities of forced water-oil cooled machines. The forced air cooling can be enhanced exactly by high speed flow (turbulences are induced, thus increasing the heat transfer coefficient) and very high temperature difference. Unfortunately, the density of air in altitude is very low, as is its the pressure. This makes it even more challenging.
However, to sum up, this is the aspect I will be looking at in the future. Say hello to CFD Nick!!
Q: I feel your pain. How’s it going?
A: I have already possible designs optimized structurally for best weight/efficiency trade-off, but with current densities of 15 A/mm^2. That’s a value that can be done only with water or oil cooling on the ground. If we can push this current with only air cooling we win. General Electric seems to be already there (they have a 7.5 A/mm^2 performance with 13kW/kg at 97% efficiency air cooled), but come, on they have billions, and a huge engineering team. Designing this machine in my Uni is, well, me…for the moment 🙂
Furthermore, the are lots of other issues, like insulation problems due to low pressures in altitude, higher iron losses due to low temperatures, use of less powerful SmCo PMs because of harsh environment…
Induction motors
Q: Based on the published literature, 15 Amperes per square millimeter is really good even for a liquid-cooled machine. For an air-cooled one it’s simply amazing! So I think you’re doing quite okay to say the least. But let’s move on. Let’s talk about induction motors.
A: The IM is very attractive since it is very cheap. Not only that, but it is very robust too! It is not very efficient for small powers, but it becomes so for very big ones. The actual best high speed/high power machines in industry are either IM or SPM machines. Of course there is the other huge benefit of self starting capability, because of a non zero torque at zero speed at connection. However, given the decoupled frequency in the aerospace components I fear this feature is not really exploitable.
I will definitely investigate the IM more at some point, but mainly for comparison purposes. We are quite convinced, at least my research team, that the most powerful way to go is with PMs. Remember also that for mechanical clearance tolerances and other issues the mechanical air gap must be large, no matter the machine topology. Therefore, the IM quickly loses torque density, as well as plunges in power factor figure. Another issue is the eddy current losses in the rotor. However, we have found that fractional slot solutions for PM machines can give even higher rotor losses than the IM counterpart, which is more dangerous for PM demagnetization.
At the moment a conventional SPM with integral/distributed winding solution with a relatively high number of poles seems to be the way. Halbach arrays are also not a good solution. This is because, the Halbach array start to be convenient when the rotor back iron almost disappears due to the closing flux within the PM themselves. This can happen only when the PM height is big enough (unless an impossible number of segments is made). A too big a PM thickness compromises even more the rotor integrity, requiring an unreasonably wide sleeve, killing in the end the torque.

Winding losses
Q: That’s interesting, considering how often Halbach (love how the term sounds like a scifi weapon btw) arrays are used in lower-speed high power-density machines. Anything more?
A: I’ve one final thought for the modelling. My optimization at the moment needs a long time because I need to simulate at least an entire electrical period, or two. This is mainly for the losses, because otherwise the torque is well known in average and ripple both just after 1/6 of the cycle (steady state constant speed I mean of course). However, I am making my computation faster. In case of fractional slot with particular combinations (3 slots / 2poles for instance) only one sixth of the period is needed, after some simplifying hypothesis, to get everything (losses, torque and so on). For integral slot half a cycle may be needed for an initial analysis. So I hope to make my optimization faster. But as I said, the main challenge will be the fluid and thermal dynamics analysis.
As I know you, Antti, you could be interested in how I consider my winding losses. I can say that I consider a Litz wire transposed design within slots. This should reduce at minimum our beloved circulating currents. Even if costly, usually the aerospace sector has a lot of money, and if a solution is effective they go for it, no matter the price. To take into account, quite roughly, the skin effect and proximity, I use the Sullivan’s method of the derivative of the squared B field, according to a possible strand positioning within slot. This is of course a post-processing, but after all you are the expert for the real embedding in the solver, not me 🙂
For doing this it was very tricky to bypass the commercial software bounds and access mesh, nodes, potentials to do whatever I wanted with them. But, I did it, and luckily I did my thesis with you in Aalto, so I got familiar with FEA. 🙂 So thank you for that!
Q: I also think the B-squared approach is a great compromise between complexity and accuracy. Although I never use it in the original form of Sullivan. I mean, he basically defines a set second-order mappings from currents to losses, and then computes the losses as a superposition. This is, in my opinion, an unnecessary step, since after an FEA simulation you do have the entire field solution. So, you can simply post-process the losses from that.
And finally, thank you for making such an awesome sales point for me! That’s indeed the problem with commercial software – you are more or less bound by them. By contrast, if I want to do something weird with the solution or the model, I can. Case in point, I can access the field derivatives needed for loss computation in maybe two lines of code, even though I don’t have that model as part of my standard library yet.
But in any case, thank you so much Nicola for the interview, and all the best for your research!
A: My pleasure.
Have a question to Nicola or I? Hit us up in the comments below, and make sure to connect with him on LinkedIn too!
Check out EMDtool - Electric Motor Design toolbox for Matlab.
Need help with electric motor design or design software? Let's get in touch - satisfaction guaranteed!
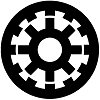
What is the meaning of electric aviation?
Well, there’s something of a sliding scale there. After all, even the planes we have today utilize electric actuators in ever-increasing degree.
However, I guess for a plane to be ‘truly electric’, a significant portion of the effective thrust would have to be produced electrically.