What are active magnetic bearings, and how do they work?
Are you familiar with active magnetic bearings? Recently, my path has repeatedly crossed with them. Hence, I thought why not introduce you to them as well.
Note: this post was largely written on my mobile, during the PEMD conference. Spot a typo – get a virtual cookie!

AMBs briefly
Active magnetic bearings, or AMBs, are exactly what their name suggests:
- They are bearings, used to enable rotation. (Typically, the same principle is often called levitation when used with linear motion.)
- They utilize magnetism, and
- They require active control to work.
Let’s consider an electric motor as an example. The motor has a rotating rotor, mounted on a shaft. To enable the shaft to rotate, it of course has to be supported by bearings. Often, these are mechanical ball or needle bearings.
However, mechanical bearings have several drawbacks. They require maintenance, and fail relatively often compared to other components in the system. Finally, they generate some losses, and can generate and transfer vibrations.
By contrast, active magnetic bearings would levitate the shaft, without any mechanical contact into the shaft. Due to the lack of mechanical contact, magnetic bearings are very durable. Furthermore, they of course generate very little friction (although they do incur losses elsewhere).
Finally, they allow adjusting the axis of rotation. This can be very beneficial if there is a slight mass-imbalance in the rotor (which is the case almost always, to some degree). In this case, the rotor can be allowed to rotate along its center of mass, rather than its geometric center, eliminating the mass-imbalance vibrations altogether.
How AMBs work
Alright, they are obviously great in many ways. But how do they work, really?
Luckily, the answer is really simple, based on the attraction between an electromagnet and a lump of iron. In fancier terms, reluctance force.
In this case, the lump of iron is the shaft, or a special small non-slotted rotor attached to the shaft. Correspondingly, the electromagnets form the non-rotating stator of the AMB system.
So, in simplistic case, we’d have a single electromagnet above the shaft, pulling it up so that it floats mid-air.
In reality, things are of course a little more complex than this. The stator typically resembles the stator of an electric motor, with four or more teeth and coils. This provides a closed return path for the magnetic flux (as opposed to the single-electromagnet example), greatly increasing the generated force.
Furthermore, it enables producing force also in the horizontal direction. Although this may not be required for levitation (unless the motor base is tilted), it can be used to control and prevent vibrations in this direction.
Why are they active?
The configuration above is of course is not stable by itself. The attractive force from an electromagnet is inversely proportional to the distance – getting stronger the closer things are – so the shaft would slam into the AMB stator after the slightest disturbance.
For this reason, AMBs feature position sensors for the shaft, and a controller adjusting the currents accordingly. Simply put, if the shaft drifts right, left-ward force is applied, until it’s again aligned. Of course, the force is rarely just on-off – this could result in large vibrations as there isn’t much damping. Instead, it’ll be adjusted based on the magnitude of displacement, using either a simple PI controller, something infinitely more advanced, or something in between.
The frak is a bias current?!
One more detail. Often, AMBs utilize a bias current configuration.
Let’s say we have four teeth&coils in the stator: two vertical (up/down) and two horizontal (left/right). As the reluctance forces are purely attractive, it would seem that we need to be able to supply each four coils independently. Supply current to the top coil to pull upwards, and so on.
However, this is not the only option. Instead, we can first supply a constant bias current for all four teeth. For a centered shaft, this results in no net force, as the individual tooth forces cancel themselves out.
Next, we can add some control current, let’s say in the two vertical teeth. This current flows in a control winding, oriented in such a way that it opposes the bias current in the bottom-most tooth, and adds up to it in the top tooth. This, of course, results in a net force pointing upwards. And vice versa, a negative force is achieved by reversing the control current.
In this way, we need only one DC current for the bias, and two adjustable control currents. So, the construction is somewhat simplified.
Furthermore, the force produced by each coil is proportional to square of the total current flowing in it: bias current plus/minus control current. Due to this, and the fact that all the coils are producing bias force at the same time, we can get proportionally sharper changes in the force with the same change in control current.
Conclusion
Active magnetic bearings levitate the shaft using magnetic attraction, aka reluctance force. They are contactless, and thus offer smooth rotation with little to no maintenance.
Check out EMDtool - Electric Motor Design toolbox for Matlab.
Need help with electric motor design or design software? Let's get in touch - satisfaction guaranteed!
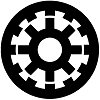
Seriously, the BEARings are awesome 🙂 I actually have an FEA kitten on my blog :p
This is what I love about your work Antti – the fun! Well… I don’t understand much more in all honesty – I finished magnetics in my primary school I think. All I know is that “Opposites Attract” (https://www.youtube.com/watch?v=xweiQukBM_k)!
I remember the FEA kitten, it’s adorable!
And don’t worry, magnetics doesn’t get any easier with further study. “Opposites attract” is pretty much as good as it gets.
Hi Gentlemen,,,just came across Annti`s website…in fact one of the key players in AMB`s i actually based in Lappenranta, Finland..Company is SpinDrive Oy. Take a look and get in touch with our office there or me in case of any questions 🙂
Happy to be of service!!
Norbert