Interview with Aegis Power Systems
Hello all, and welcome to this interview series on all things motors. Here, we’ll be talking to different people working on electric motors, EVs and e-mobility, power supplies, charging, and all things associated.
So, anybody making waves, expect to see them in here.
First in line we have Arlissa Vaughn from Aegis Power Systems. Without further rambling, let’s get on with it.

Background
Q: First, can you tell me a little about yourself? Who are you, and how did you end up doing what you do? And what is Aegis power in the first place?
Aegis Power Systems, Inc is a USA-based company concentrating in the design and manufacture of power supplies. We were formed in 1995 and have good success in the defense industry, providing a variety of power conversion equipment for everything from embedded computer to electronic warfare to military aircraft and vehicles.
I’ve been with the company since 2014 and my focus is more on business development and sales/marketing, although as CEO of a small privately-held business my hands tend to be in a little of everything at any time.
Defense
Q: You mentioned having done some work on defense automotive vehicles. Anything you can share on that? What kind of vehicles, and any performance specs you can share? What about the application environment in general? I would expect that military equipment needs to be able to take quite a pounding. I mean, reliability issues can literally be a matter of life and death, plus the most sophisticated tool available on the field might be a hammer.
We have developed a few standard products for military EV/HEV application – some for power conversion from the battery to the electric payloads and some for other types of onboard power. All are designed to withstand a variety of rugged conditions including ingress protection, shock and vibe, and wide temperature range. Additionally, defense has tight regulations for EMI and noise. Our specialty is in custom power supplies, so most of our projects have unique features or design constraints. The challenges change regularly and force our team to continually gain new perspective to share with customers.
EVs

Q: Alright, let’s talk EVs in general. How important is power conversion, and what challenges are there? After all, one might think that power electronics are already quite lightweight and efficient right now. Does power conversion matter to the overall EV design?
The electrification of vehicles took the automotive industry by surprise as consumers demanded features at lightning speed. As you already pointed out when we were first introduced, power conversion has not traditionally been in the automotive engineer’s handbook of expertise. So as these demands have grown, so has the demand on power conversion engineers.
A typical HEV system involves not just one, but several, pieces of power conversion equipment. These may include a DC/DC converter coming from the high voltage battery pack, several buck or boost converters from a 12V battery source, an inverter for power coming from the motor, several inverters for various equipment like air-conditioning, and a battery recharging system.
In military and industrial applications, the onboard equipment may require 10kW or more power to support the add-ons. On a consumer grade vehicle, these demands are more in the range of 4kW or more, depending on model. That’s quite a lot of power, potential heat, and performance requirement.

Q: You mentioned the topic of EV lightweighting, and I think it caught the attention of most of us. Can you go a little deeper into that? How do you typically approach the goal?
Of course, you know that light-weighting any EV/HEV vehicle means better energy consumption and longer battery charge. The industry first began light-weighting in the obvious places – changing out materials and eliminating components. Now it’s starting to look at the electronics.
With respect to power conversion, the higher the efficiency of the power conversion, the longer the battery lasts. Then you also get secondary improvements as the increases in efficiency equate reduced need for thermal mitigation, so a lot of components start dropping off the Bill of Material and the power conversion item becomes more lightweight.
In a world where performance is key, like in racing, this becomes easier as there are fewer features required. But in a world where consumers ask for more and more features, the overall power consumption increases and the power electronics engineers are asked to bring advanced technologies such as SiC and GaN to the table. In recent years, there have been large gains in efficiency and weight reduction, but if Moore’s Law is true then we will continue to see further gains as power electronics engineers delve deeper with new materials and circuitry.
Motors
Q: Finally, for reasons obvious, let’s take a motor-focused view. I would think a modern EV has quite a few of them, from the obvious drive motor to steering assist, electric windows, AC fans… I know many motor designers treat the power supply-side as an ideal voltage source, while for the power-electronics people the motor is often seen as a simple LR circuit. Do you think a more co-op approach would be beneficial? And how do you do it at Aegis? Do you have motor specialists in-house, do you collaborate with motor manufacturers, and so forth?
Great question, and this shows your insight too. For every industry we’ve ever worked with (not just automotive), the power supply often remains the last piece of the puzzle. This usually means the project is down to crunch-time and the power engineers are expected to quickly fill the need of an advanced system. To avoid this mad dash, we cultivate relationships with customers and encourage system designers to reach out to our team early in the design/bid process to determine feasibility or consider trade-offs. A cooperative environment is ideal to creating an ideal system. We have not collaborated directly with motor manufacturers yet, but would welcome this opportunity as a mutually beneficial arrangement with useful impact to the industry.
Conclusion
Thank you, and thank you for the interview! I certainly learned quite a bit, and I hope anybody who reads this post learns, too.
To get in touch with Aegis Power Supplies, you can either head to their website linked here, and I don’t think Arlissa will mind a LinkedIn message either.
Now, it’s your turn. Have comments or questions – let us hear below!
Check out EMDtool - Electric Motor Design toolbox for Matlab.
Need help with electric motor design or design software? Let's get in touch - satisfaction guaranteed!
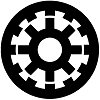
This is interesting. Am learning that power has important role in EV. Thanks Antti