The number of poles (of an electric motor) has become something of a pet peeve of mine.
Many beginners get it totally wrong – hello me back in 2010 or so! More about that shortly.
And even more are at least somewhat confused about it. While you can rarely go wrong by simply asking those who might know more (the Electric Motor Design group on Facebook is a great place for that), you might also wanna read this post first.
So let’s have it – the Good, Bad, and Ugly of increasing the number of poles.

The Ugly
Let’s begin with the Ugly.
Poles ARE NOT gears.
What this means is that even though there is a definite inverse relationship between the pole number and speed, there is no corresponding increase in torque.
In other words, doubling the number of poles does not (in general) double the torque. The pole number does not act like the ratio of a mechanical gear. It directly influences the speed, yes (assuming fixed supply frequency), but the effect on torque is much more shady and flexible.
The way motors are often taught and learned might be to blame for this confusion. The basic underlying physics are skimmed over, either by the teacher or the student, or more likely both.
To perpetuate the error, many textbook torque formulae do have the pole number as a multiplier. What they don’t show, however, is a corresponding division also hidden somewhere else.
For instance, let’s say we keep phase current and mechanical speed (and airgap flux density) the same and double the number of poles. The flux per pole gets halved, but this is immediately compensated by the fact that we have more of them in series. As each pole is now smaller, we can only fit half as many turns in each of them. This would imply a reduced back-emf and power (and thus torque) if not for the fact that the electrical frequency is now higher, too, again compensating for this **.
** I now realize this example is perhaps a little too simplified and/or misleading. For instance, the inductance of the stator is proportional to the number of poles squared. Meaning, for motors that are excited from the stator, their ability to produce flux also takes a hit with increasing pole count. Meaning, the airgap flux density might not stay the same either, unless other dimensions are changed, too.
This is very clear in synchronous reluctance motor, where the airgap flux density is defined by the stator and stator alone. Double the number of poles, and flux density gets halved, unless you change e.g. the current density or geometry in other ways.
Induction motors – which I coincidentally kinda hate for this reason – are more complex. In IMs, the airgap flux density is defined by the combination of the stator current and the induced rotor currents opposing it. (In the equivalent circuit, this is seen as part of the stator current escaping through the rotor branch and skipping the magnetizing branch.) Thus, increasing the pole count of an IM means that a larger share of the stator current is spent on exciting the motor, leaving proportionally less to link the rotor and produce torque.
In other words, the motor would produce exactly the same torque no matter the pole count, if all other dimensions were kept intact.
Now, let’s proceed to the actual comparison.
The Good
End-winding length
More poles results in reduced end-winding length* and therefore reduced copper losses.
*While why this happens is quite basic knowledge, here’s a beginner-friendly version: Think of a two-pole machine. The end-winding – the winding part outside the motor core between two successive coil sides – has to cross roughly half the motor periphery. For four-pole machines, the distance is reduced to one fourth, and one sixth for six-pole machines, and so on.
Furthermore, reduced EW length also reduces the total motor length. This, obviously, can be a nice thing on its own. Or, alternatively, the core length can be increased to obtain more torque from the same space envelope.
Increased torque capacity
Increasing the pole count can increase the torque capacity, under certain conditions.
This happens thanks to the reduced flux per pole, allowing a thinner stator (or rotor) yoke. This can in turn translate to a larger airgap radius or/and deeper slots, both of which lead to increased torque.
However, this is where the aforementioned conditions come in.
First of all, the airgap flux density must stay the same, or at least not drop much. In induction and reluctance machines, this may not be the case. But more of that later.
Similarly, the total current in each slot (NI) must also stay approx the same, or increase. Again, this might not always be the case due to increased iron losses (more again later).
Increased peak torque capacity
Which brings us to our next point. Increasing the number of poles can also allow much higher electric loadings (NI per slot pitch, essentially) to be used.
Remember, the torque is proportional to NI times (useful*) airgap flux density. This does not depend on the pole count.
*The part of the airgap flux in phase with the rotating current density wave. Think sines and cosines here.
What does depend, however, is how much “extra” (non-torque-producing) airgap field is created by the current. Indeed, the share of the airgap field generated by the stator is essentially the total current in one pole divided by twice the airgap length.
So, oversaturation of the stator and rotor core may become the limiting factor before thermal or other aspects, especially when peak torque capacity is considered. Increasing the pole count can help in this respect (although it does not help with other problems associated with peak operation, like leakage fluxes or end-winding forces). Double the number of poles, and you halve the stator winding’s ability to create flux.
Which brings us to our next point.
The Bad
Magnetization
The previous point applies when stator oversaturation is an issue at the peak torque levels. However, in induction and reluctance motors, the entire airgap flux is generated by the stator winding.
And just moments ago we learned that the higher the pole count, the worse the stator performs at magnetization. For this reason, you rarely see induction motors with many more than 8 poles, and reluctance machines are lucky to reach 6.
AC losses or speed
Like discussed earlier, increasing the pole count reduces the synchronous speed of the motor. Meaning, if we wish to maintain the speed, supply frequency must be increased.
This will increase the iron losses, and AC losses of the winding. Furthermore, even inverter design may become problematic if we move to very high numbers.
On the other hand, if we do reduce the rotor speed, we may very well lose some power. As we’ve learned, increasing the poles can help increase the torque, yet this might still not be sufficient to compensate* for the speed reduction.
*power equals torque times speed, remember
Interpole leakage
Complex stuff, meaning that some of the rotor flux escapes from one pole to another, without linking the stator winding at all.
Normally, it’s ranges from ‘negligible’ to ‘nuisance’, but it also doesprevent absurdly high pole numbers from working.
Manufacturing
Generally speaking, higher pole numbers lead to more difficult manufacture.
This is more of a trend than a hard-set rule: for instance a concentrated winding for a 10-pole motor can be easier to make than a distributed winding for a 2-pole one. But even then, a 40-pole concentrated winding is kinda more complex than the 10-pole example seconds ago.
Conclusion
- Poles are not gears. A higher number does reduce the synchronous speed, yes, but it is not automatically accompanied by a corresponding increase in torque.
- Nevertheless, a higher pole count can increase the torque capacity. This is especially true for PM machines.
- Motors excited from the stator typically don’t perform well with too many poles.
Check out EMDtool - Electric Motor Design toolbox for Matlab.
Need help with electric motor design or design software? Let's get in touch - satisfaction guaranteed!
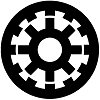
Thank you, Antti! For yet another interesting post on electrical machines.
One question regarding this statement: “The flux per pole gets halved, but this is immediately compensated by the fact that we have more of them in series. As each pole is now smaller, we can only fit half as many turns in each of them.”
Does e.g. splitting the pole in two smaller ones really limit the space for pole windings in the same ratio? So if we use same size field winding conductors could we not use more effective turns in two poles that what would be fitted on one pole?
Thanks for your writing again and hope to see more to come.
-Olli
Thanks Olli! Yes, I now realize the poles-turns-flux example was perhaps a little too simplified, in many respects. Especially in the case of field-windings in salient-pole generators, the relationship is likely very much nonlinear.
Likewise, my use of ‘turns’ was perhaps unclear. Ultimately, what it boils down to is more or less the electric loading, i.e. the number of Ampere-turns per unit airgap circumference.
So, for two pole-pairs, the number of total (Ampere-)turns would almost certainly be higher compared to one pole-pair, but the number of turns per pole might be lower. I write ‘might’, because the space constraint might not be that significant for such low pole counts (if we’re still speaking about field-windings). However, if we were to consider say 16 pole-pairs, there the space limit would really start to count.