Differences of switched and synchronous reluctance machines
Saw the earlier post about the differences (if any) between BLDC motors and permanent magnet AC motors? Well, in any case, this post aims to do the same for switched and synchronous reluctance motors!
And even better, a follow-up post in the near future will also brush a little on performance issues. Meaning, which motor type is better. However, please don’t expect to find definite answers there. There are far too many variables for that. You will see it yourself, soon enough. Nevertheless, you will learn the grounds on which such comparison can be made for a specific application – simple design approaches, and factors to consider.
But first, let’s begin with some definitions.
What is an SRM?
Of all the different electric motor topologies, a switched reluctance motor (SRM) is the easiest one to explain to a layperson. After all, most people have a rough idea of wrapping some wire around an iron nail to make an electromagnet, and then using it to attract another nail.
Then, fixing the latter nail to a rotating shaft and surrounding it with several magnet-nails essentially gives you an SRM. Fire the magnets (and turn them off again) in a sequence, and the nail will rotate.
Sidenote: explaining the need for back-iron to a layperson can be more complex, but a few metaphors and comparisons can do wonders. Pipes and waterflows are my favourite at the moment.
And that’s exactly how traditional SRMs work. There are normally at least two independent sets of coils, controlled be their own power electronics switch. They can be called phases too, but it must be noted that the current in each phase is essentially unipolar. Meaning, it never flows to the negative direction; only positive or not at all.

There are many, many ways to make a SRM. The most important characteristics are the number of rotor poles and stator teeth. But, even with those fixed, there can be some freedom left in the winding design. For instance, one can wind coils around every tooth, or thicker coils around every other tooth. These types are called single and double layer windings, respectively.
Benefits and drawbacks
The number one benefit of a SRM is its robustness. The rotor is almost as simple as it gets, meaning it can survive high stresses and rotation speeds. Also, there’s no risk of demagnetization (as opposed to PM machines), and the rotor losses are small (compared to induction and wound-field machines) making cooling issues simpler. However, these latter two points apply to SynRMs too, as we’ll see later.
SRMs also get touted for their good power density, but that is not something I’m immediately convinced of. We’ll come back to that.
There are some drawbacks, too. Switched motors can be noisy, due to the large radial forces pulling on the stator teeth.
Furthermore, actually accomplishing the aforedescribed on-off switching of currents can be problematic. You see, once a rotor pole is fully aligned with a stator tooth, the corresponding coil has to be de-energized (switched off) quickly. Otherwise, it will start producing negative torque as the pole slips out of alignment.
Unfortunately, when the pole is aligned, the inductance of the stator coil is at its maximum. This means that a high voltage is needed to drive the current to zero quickly enough. Meaning, you’ll either need a large enough voltage reserve (to recover the energy in the magnetic field) or sturdy power electronics to survive the voltage peaks from hard switching (dumping the field energy as resistive losses). Or, use some exotic bridge configuration that I’m simply unaware of.
But I digress. On to SynRMs.
What is a SynRM
Synhcronous reluctance machines (SynRM) also operate on the attraction between an electromagnet and a lump of iron, so to speak. Indeed, you could also make a SynRM out of the coils-and-nail example we saw earlier. The only difference would be in how you feed the coils. Indeed, rather than switching the coils on or off completely, you would feed the sinusoidal AC currents, each coil with a suitable phase shift of its on. The nail-rotor would then align itself with the resultant magnetic field of all the coils.
In practice, however, SynRM rotors are much more complex than a nail. Instead, they often look like below. More like a set of bent nails stacked together, if you want to go carry on using the nail example.

The complex structure serves a purpose. Specifically, the goal is the make it as easy as possible for the magnetic flux to pass through the rotor in one direction, along the black fishbone-like iron paths (called d-axis), while preventing it from crossing it to the other – perpendicarly (called q-axis)
The latter reason also explains why you see so many of those iron paths (flux guides) separated by air (flux barriers), instead of a single big one. You could indeed squeeze all the guides into a single lump to get pretty much the same d-axis behaviour. However, that big lump of iron would also offer an easy part for the q-axis flux near its tips, killing the motor performance.
Another difference from SRMs is the stator structure. Remember, in SRMs the number of stator teeth is directly tied to the number of rotor poles, as well as the winding configuration. By contrast, SynRMs usually have “normal” stators that you see in all kinds of electrical machines, with usually as many slots and teeth as possible.
Benefits and drawbacks
In terms of pros and cons, a SynRM is pretty much the opposite of a SRM in many respects.
It is often much less robust, due to the fact that the flux iron bridges connecting the flux guides to each other need to be as thin as possible. Furthermore, the rotor can be costlier and/or more complex to manufacture.
On the other hand, there are no particular issues with noise or power electronics. Many sources list a low power factor as an issue with SynRM, which is technically true – compared to e.g. permanent magnet or wound-field synchronous machines. However, from the performance point of view the same is, in a way, also true for SRM. Meaning, both machines need to generate the magnetic field with stator winding currents, incurring losses in the process.
Conclusion
The basic differences between switched (SRM) and synchronous (SynRM) reluctance machines were covered:
- SRMs can be noisy and hard to supply.
- SRMs have robust rotors.
- The number of rotor poles is closely tied to the number of stator teeth in an SRM.
- SynRMs are very much like the other, more traditional motors, and can be supplied with standard inverters or even the grid.
- SynRM rotors have to be carefully designed mechanically, and can be expensive to manufacture.
Next time: let’s look at some simple methods to evaluate their performance and figure out which one is better for your application.
Check out EMDtool - Electric Motor Design toolbox for Matlab.
Need help with electric motor design or design software? Let's get in touch - satisfaction guaranteed!
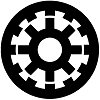
Intresting Antti…
Looking for performance comparison..specially at low voltage, high current, high speed machines..typically used in aerospace and automotive domains widely..
Thanks! I think already on LinkedIn, but in any case let’s see if I can spool something simple up in the near future!
you reference rotor manufacturing expense as being a barrier in synchrel devices, but the material costs should be lower than comparable induction devices as you only need electrical steel. Does the reluctance anisotropy require production tolerance that raise labor costs, does it require bespoke capital investment, or was the rotor expense comment just in relation to the SR motors? What’s the cause of the manufacturing expense?
Can’t really remember anymore what I was thinking while I wrote this, but it was probably indeed compared to SRMs.
At least, more material needs to be cut off from a SynRM rotor. If laser-cutting for small batch production, this means a longer time spent cutting each sheet. In series production, a more complex cutting tool needs to be manufactured. But, these are just guesses of mine – detailed production economics is beyond me.
you wrote this on my birthday, I just turned 15 that day, oh when life was simple.
Nice, I can imagine!