When to care about additional winding losses
We academics are often accused of being detached from reality. And I understand the reasoning behind. Often, what we do can be considered technical/scientific nitpicking, with few practical applications in the foreseeable future. However, just as often, this is not the case.
I exist in a happy medium. I’m an academic alright, but I also have regular contact to the industry, from sharing measurement data to consulting and training. Thus, I do have some insight to how things look like on the other side of the fence.
Thus, I thought I’d like to clear some of this academia-versus-industry confusion on my part. In particular, I will consider computation of winding losses in an electrical machine. When is it alright to invest in an advanced algorithm and/or computational power to predict them in a reasonable time, and when rules-of-thumb and measurements would serve you better?

Winding losses
Alright, you are designing an electrical machine. There are a million standards and specifications to fulfill, and quantities of interest to compute.
One of them would be winding losses, of course. You know how to calculate the DC-resistance from the winding dimensions, and you know you can multiply that with the square of the current to get an estimate of the losses.
But, you also know that in reality the losses will of course be higher. You have skin effect due to the alternating field, and you may also have air-gap flux penetrating into the slot and increasing the loss density near the slot opening. If you have a stranded winding, you most likely have some circulating current losses, too.
Now, the big question is, should you care? Should you invest time and resources into trying to determine those additional loss components? Or should you just wing it?
Below, some ideas.
When you should NOT to care about additional losses
You simply don’t care
All you want is to get a possibly-crappy machine done and shipped. Alright. I’m not gonna argue with that.
You have an established product line
Let’s say you are producing run-of-the-mill induction motors for industrial purposes – perhaps for literally running a mill. You have several decades of collective experience and rules-of-thumb on making machines.
In that case, you probably know your losses more accurately than any simulation ever could. They are your machines after all. You own them, in the figurative sense as wll.
I’m not gonna argue with that, either.
Additionally, your business is probably infinitely more about supply chains and customer relations, rather than some tenths of percent of efficiency gained or lost. They won’t make your business.
Alright, you could argue that things are slowly changing due to the new efficiency standards…But I digress.
When you SHOULD care
Your competitors do
Even though winding losses probably won’t make your business, occasionally they might break it. Let’s say you don’t care about eddy currents, but your competitor does. For basic machines, this might make their products a little better. Not too significant on its own, but still a more competitive edge.

You make special machines
However, things change when you don’t work with basic machines any more. Special machines often have special requirements.
For example, high-speed machines typically have stranded windings with lots of parallel conductors, prone to circulating and eddy-current losses both. Multi-pole permanent magnet machines as well, especially when made for low-voltage applications. Vehicle motors, anyone?
Another example could be the fan motors for PCs and other electronic components. The trend with them is, they’re getting smaller, and their speeds are getting higher. Meaning the supply frequencies are getting higher, meaning the AC losses are getting more prominent. Combine that with the reduced size, and winding losses are suddenly very significant indeed.
You chase performance
I’ve stated this many times before, but I’ll state it again: efficiency is boring.
Electrical machines are already quite efficient. Pushing the envelope a little bit further won’t do much, energy-consumption-wise.
However, performance is not boring. A winding with reduced losses is a winding that can be smaller. Or a winding that can have more current rammed through it. Both options make for a more power-dense machine.
You chase excellence
The world of electrical machines is quite conservative, to say the least.
Accordingly, the stardard operating procedure, when faced with stranded windings let alone random windings, seems to be to keel over and die.
In other words, only utilize rules of thumb combined with measurement data. Which, admittedly, has been good enough for now.
But today, the things are slowly changing, at least in my humble opinion. Performance and efficiency requirements are getting higher, and the contribution of winding losses is getting more significant due to the wider spread of once-special machine topologies. At the same time, the time from the design board to a final product is getting pushed shorter.
To thrive, good enough is no longer good enough. If your machines are not getting better, someone else’s certainly are.
Conclusion
Have something to add?
Please comment below!
-Antti
Check out EMDtool - Electric Motor Design toolbox for Matlab.
Need help with electric motor design or design software? Let's get in touch - satisfaction guaranteed!
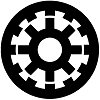