How Frequency Response Analysis is used in electromechanics
Remember FEAforAll? In case you don’t, click the link (opens up in a new tab) and come back here afterward. In case you don’t want to click the link, here’s the short:
FEAforAll is another blog on finite elements, focusing on structural mechanics. It also follows a much more professional approach than mine. So in case you don’t want to read about biceps and cheesecakes every once in a while, you might be better served by FEAforAll or Enterfea.
Frequence Response Analysis
In any case, this week FEAforAll published a nice post about frequency response analysis. You can check out the post and its awesome graphics by clicking the figure below.
So check it out, and then come back here to read my thoughts.
Back already? Great!
Frequency response analysis is pretty much exactly like what the name suggests. We poke at the system at a certain frequency, and see how it responds.
In mechanics, this often means that we have force oscillating at a certain frequence, and we see how the system vibrates.
What about Motors?
We also do frequency response analysis (let’s use FRA from now on) in electrical engineering. Most often, it’s exactly what Cyprien described behind the links – meaning mechanical oscillations.
For instance, it might be computing how the stator of a motor vibrates due to the rotating pulling and pushing forces from the air-gap flux. If it reacts too strongly, it gets squeezed like giant donut. It won’t break, but it will make one hell of a noise.
Or, we might be interested in the bending modes of the rotor. Like turbogenerators in power plants. They can have really long shafts with no bearing support in the middle. So, they might react really strongly to something as low as 50 Hz excitation. That means lots of bending vibration. And that can mean the rotor hitting the stator.
And when a 500 MW generator suffers any kind of collision, things do break down.
Or, we might be interested in a high-speed machine instead. Those are really short, and hence have high natural frequencies. But, they also rotate really freaking fast – 60 000 rpm is common. Something like that is often beyond the first natural bending frequency, requiring quite sophisticated speed control to avoid disasters.
Let’s Twist Again
My third example is something our professor has studied quite a bit – torsional vibrations.
That might mean twisting the shaft along its axis, but even that’s not required. Remember we are talking about rotating machines here.
Actually, the rotation itself corresponds to the simplest twisting mode of all – rigid motion.
Alone, it wouldn’t be very interesting from the FRA point of view. It would simply rotate and that’s it. But, we are not dealing with a passive system.
It’s called electromechanics for a reason. There’s a very strong coupling between electromagnetic (the torque production) and mechanic (the rotation).
In this case, we can compute another kind of frequency response function.
Indeed, we use, the speed as input, and the torque as output. In other words, we add some sinusoidal oscillation to the rotation speed of the rotor, and see what kind of oscillation we get in the torque.
Or, we can go even further than that – and add ALL frequencies to the rotor speed at the same time. In other words, use an impulse function. Of course, that’s numerically quite difficult, but even an approximation yields a nice range of the total frequency response.

We can quite easily establish a correspondence between the response, and the electromechanical damping. And it turns out that under certain conditions the damping can get negative.
Meaning the motor starts to feed more and more energy to the oscillations.
And things break down.
Please comment and share! 🙂
-Antti
Check out EMDtool - Electric Motor Design toolbox for Matlab.
Need help with electric motor design or design software? Let's get in touch - satisfaction guaranteed!
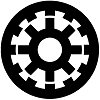
needto fast respon about these things dude, can i share it?